Machining through plastic... and an earthquake
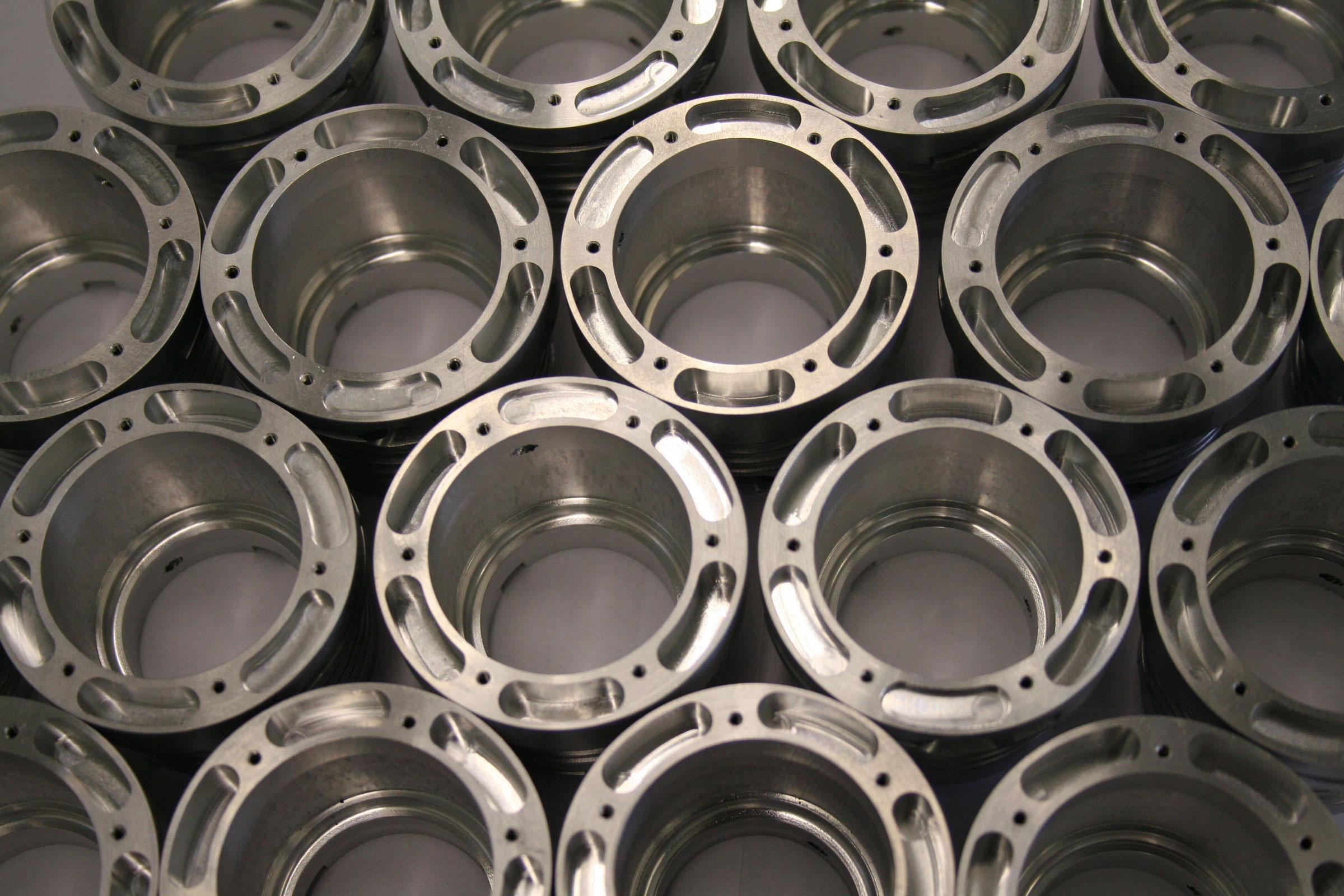
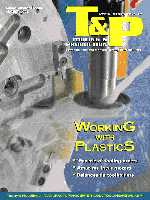
While walls shake, tools keep part in spec
A material called FR4 is a glass-filled plastic, difficult to machine and very abrasive on tooling. It is one of several materials used by Fluke Metal Products Inc. in Bothell, WA, to produce precision devices for avionics, medical equipment, surface mount technology and electromechanical inspection systems.
On a typical production day earlier this year, a 12´´-diameter flat ring of this FR4 material was being machined with an IBAG HF100 high-speed spindle integrated in a Compumachine Vibra-Free vertical machining center.
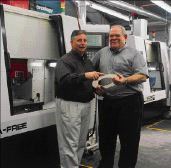
Four-hundred square pockets, each 0.022´´ x 0.022´´ x 0.065´´ deep, were being milled at 45,000 rpm using a 0.10´´ diameter carbide end drill. By way of a size comparison, that tool's diameter is about three times the thickness of a human hair.
The machining conditions were challenging enough by most standards. Then they got tougher. An earthquake hit--literally. Mick Crotts, CNC operator at Fluke, comments on what happened next:
"I was well into the job when the earthquake hit. It was big--a 6.8 on the scale. The room was shaking, the lights started swinging, I thought the building was going to come down. We all ran outside and waited until it was over. When I came back in, the machine was still running at 45,000 rpm, milling the tiny pockets. The cutter hadn't broken, but one of the concrete building floors had a crack about a half-inch wide and five inches deep."
When the dust had settled, Crotts took the finished part off the machine and brought it up to Quality Control (QC) for checking.
"It was amazing," he says. "The part was perfect. I can't believe the rigidity of that IBAG spindle and the Vibra-Free machine. Even though everything in here was shaking like crazy, the part came out right to spec."
History of quality
Robert Fluke is president of the company his father founded in 1957. He oversees a facility that employs 65 people and runs 24 hours a day, Monday through Thursday and two eight-hour shifts the rest of the week. Most of the people at Fluke Metal Products have exceptionally long tenure, take advantage of the overtime opportunities and display a strong sense of company loyalty and pride in their craft.
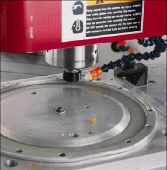
"Over the years," says Fluke, "we've evolved from a design engineering firm into a production company specializing in close tolerance components and assemblies. In addition to our CNC lathes, turning centers, machining centers and other production equipment, we have an extensively equipped QC department."
Unusual for a company of this size are six full-time QC specialists to verify the customers' specifications on all part runs. Verification printouts are provided on request at no charge. In addition, parts are deburred to a 20-power magnification as a value added service, if required.
"Quality is number one," says Fluke, "then delivery, then price. When we marry all three criteria together, then we have a happy customer that stays with us."
Need for speed
Customers do stay with Fluke Metal Products, from Washington to North Carolina, to New York and New Jersey. The company's reputation for delivering intricately machined precision components, in short batches, encouraged Fluke to take the next step--from traditional production machining to high-speed production machining.
"We needed more rpm," he says. "The speed from the machines we had just wasn't enough. Our average batch runs on the machining centers are between 50 to 100 parts. That calls for frequent changeovers and setups. We had to have faster throughput, and that calls for faster rpm and more productive chip loads. The faster we can mill the pocket, so to speak, the better we can get our prices in line with the customer's perspective. We had to go to high-speed machining to stay competitive."
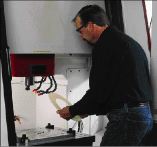
Fluke dispatched three of his top people to IMTS 2000 in Chicago to check out high-speed vertical machining centers. They quickly narrowed the field from several down to the Vibra-Free with the HF100 IBAG spindle. Featuring hybrid ceramic ball bearings, an open-loop Vector control and a chilled water cooling system, the IBAG HF100 spindle delivers up to 50,000 rpm at 8.0/12.0 hp.
After witnessing the success of their first machine, they soon had a second Vibra-Free VMC installed, also with the IBAG HF100 high-speed spindle. This machine, though, was a 5-axis model that incorporated a rotary table (C-axis) on a trunnion (A-axis), with all five axes under the machine's Fanuc 16i CNC control.
A+ tooling system
George Passino, Fluke's manufacturing engineering manager, especially likes IBAG's SKI-25 tooling system. "With a lot of other systems," he says, "you have to go to a comparator and actually dial in each of the tools to the holder. With the IBAG SKI-25, we typically just insert the tool and begin machining. Because of the quality of the holder, we rarely even check them any more. That means one less thing our operators have to do when they're constantly changing tools, changing parts, changing setups."
Passino reviewed some of the jobs currently being machined with the IBAG high-speed spindles.
"This part is made of Techtron PPS," he says, holding a tiny part up to the light to show off its fine detailing. "It's a high-heat part, one of a family of five similar parts used to guide wires in a capacitor-checking machine for the computer industry. Using a 0.015´´-diameter end mill, we take a series of eight cuts of about 0.010´´ deep at 45,000 rpm and a feedrate of 30 ipm. It's a very good test of the spindle's rigidity and concentricity since the thickness of each wall of the wire guides is only .010´´. The machining cycle is only a few minutes, compared to the 30 minutes it took previously on a more traditional VMC at 15,000 rpm."
Referring to the part that was being machined during the earthquake, Passino says they had previously tried machining the part on the 15,000-rpm VMC. Completing the job took close to four hours. With the IBAG spindle on the Vibra-Free, the job is completed in 80 minutes. That includes not only the 400 0.022´´ x 0.022´´ pockets, but also 400 pocket "tails," each 0.120´´ long x 0.015´´ wide x 0.018´´ deep. Each corner radius generated is 0.005´´. Repeatability is exact for each pocket and each tail. There is no margin for error because of the super-accurate end use of the part in a capacitor check-sort system.
On the 5-axis machine, the 50,000-rpm IBAG spindle is at work machining a capacitor insert test plate. The material is the highly abrasive, glass-filled FR4 plastic. A 2´´-diameter wheel cutter on a 3´´-long shaft cuts 18 positioning slots at 20-ipm feedrate.
"Three inches is a long reach to get to the part," says Passino, "and would make a lot of people nervous in high-speed machining. But this IBAG spindle is very rigid and does a great job at handling that long length with a big diameter wheel."
A second wheel cutter puts in 60-degree angles at 60-ipm feedrate. Then, 0.014´´- and 0.020´´ diameter long-reach end mills complete the final geometries of the slotted part. The finished parts are assembled into a circular component used in four-array capacitor testing equipment.
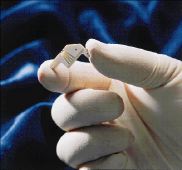
Back on the 3-axis Vibra-Free, the IBAG HF100 spindle is realizing a 30-percent time savings in machining a pair of aluminum avionics parts. Each will serve as an LCD frame with pockets for control and call-up buttons.
"All the parts we produce have a common thread," says Passino. "They are close tolerance, high-precision components that have some sort of cosmetic, value-added finish to them. Because of the precision and complexity of the components, we machine almost all of the fixturing and tooling for them right here on the Vibra-Free VMCs with the IBAG spindles. If the part has to be to 0.0002´´ tolerance, the fixture must be no more than 0.0001´´ tolerance. The fixture has to be half or less in order to give us the opportunity to hit the nominal on the part."
According to Fluke, the direction his company is taking will be more and more into the high-speed end of machining. "We have to keep ourselves positioned on the cutting edge of machining technology" he asserts, "so that we can continue to support our customers better than our competition."